January 13th, 2017
Randy Robinett, founder of BIB Bullets, is a highly respected custom bullet-maker. In recent years, Randy’s 30-caliber projectiles have won countless benchrest-for-score matches, and captured many National titles. If you want to “run with the big dogs” in score competition, campaigning a 30BR with BIB bullets is a very smart way to go. In this article, Randy talks about the process of creating highly uniform cores for benchrest bullets.
This article originally started as an exchange of posts in Stan Ware’s Bench-Talk Forum. Stan, a gifted gunsmith, converted the Forum posts into an article, which first appeared on Stan’s Bench-Talk.com Website.
How to Make Benchrest-Quality Bullet Cores
by Randy Robinett, BIB Bullets
OK, Stan “made me do it”! A while back, Stan Ware asked if I’d submit a ditty on bullet-making. Here is the “picture is worth a few words” version. Below is a photo of a spool of lead wire. This is the first step in making benchrest-quality bullets. This spool of .250″ diameter lead wire will be cut into approximately 130 pieces, each about thirty inches long.
The Core Cutter
Here’s a really neat machine built by my Uncle and BIG MIKE. This is the core cutter. We made it using scrap steel and borrowed the crank shaft out of a 1966 Yamaha motorcycle to get the desired reciprocating-motion slide. When properly “juiced”, this machine can cut more than 3000 cores per hour.
As you doubtless deduced, the “sticks” are inserted, then fed via gravity — straightness is a virtue here! The crank, for now, is powered by the human hand. The bucket contents are the result of loading the cutter and turning the crank wheel. This photo shows cores for 112 grain, .30-caliber bullets. There are about 2500 cores to the bucket.
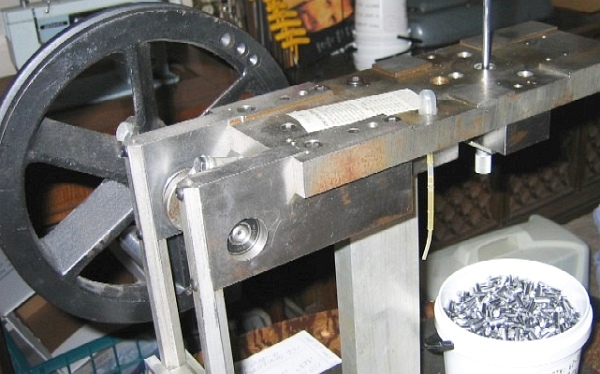
Here’s a close-up of the business end of the core cutter. Using recorded micrometer settings, this clever design allows us to get very repeatable length when changing through the length/weight cycle.
The photo below provides a closer look at the just-cut cores. Note the relatively clean shanks and square, unflared ends. This bucket contains roughly 2500 cores. By contrast, a tour of the Hornady plant will reveal cores being cut and squirted via a single operation, and deposited into 50-100 gallon livestock watering tanks!
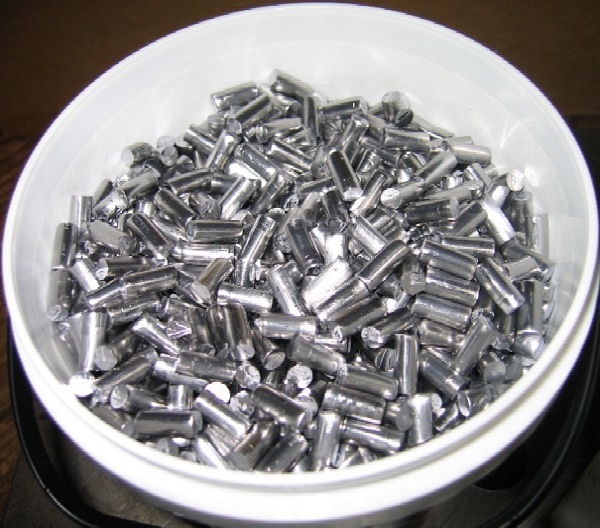
Upon my first tour of a commercial plant, I lost all feelings of guilt about the cost of custom, hand-made bullets. When one totals the amount of labor, “feel” and “culling” that goes into them, custom hand-made bullets represent one of the best bargains on the planet!
At Hornady, each press produces 50-55,000 finished bullets per 10-hour shift. By contrast, a maker of hand-crafted bullets, at best, may make 3% of that number during a 10-hour span! Yep, hand-made benchrest-quality bullets are a labor of love and should be purchased with these criteria in mind: 1) QUALITY; 2) availability; 3) price. There is no reason for a maker of hand-made benchrest-quality bullets to negotiate on price. His time is worth what one receives from the bargain!
Core-Making Q & A
Randy’s original Bench-Talk Forum posts inspired some questions by Forum members. Here are Randy’s answers to spedific questions about core-making.
Question by Stan Ware: Randy, a post or two back you said the cores were cut into 30″ lengths first and straightened. Why do you cut to 30″ lengths? What is the reason for this?
Answer by Randy: Stan, the wire is cut into 30″ lengths (sticks) and then straightened, following which it is fed into the core cutter and cut into the individual individual “cores”. If you look at the core cutter photo above, you’ll see a stick of lead wire sticking up -it’s toward the right hand end of the contraption. The cut cores are also “ejected” by gravity — the white “tickler” brushes the cores as the slide moves forward and dislodges the core from the cutter bushing.
Q by GregP: Randy, How do you straighten the 30″ sticks? Roll them between metal plates?
Answer by Randy: Greg, BIG MIKE may kill me for letting out the secret. WE “roll” the wire between an aluminum plate, which is equipped with handles, and the “plate” which you can see in the pic of cutting the wire. The straightening is really a drag. Eventually, we will have the new cutter hooked up to a “feeder/straightener” and the wire will be cut into core slugs right off the roll! Well, that’s the Dream….
Question by Jim Saubier: How much of a nub do you use at the end of the 30″ section? I imagine that every section you will lose a little from the feed end. Your cutter looks real slick, we are using the manual deal and it isn’t quick by any means.
Answer by Randy: Jim, Since I cut all of the sticks using diagonal-cutting pliers, the ends are, indeed, waste. However, only about 1/8th inch on the beginning end — the final core may be too short. I have attached a pic of my old reliable CH cutter. I still use this cutter for .22-cal and 6mm cores and, occasionally, an odd lot of thirties. The CH cuts very square ends which are free of bulges and/or flaring.
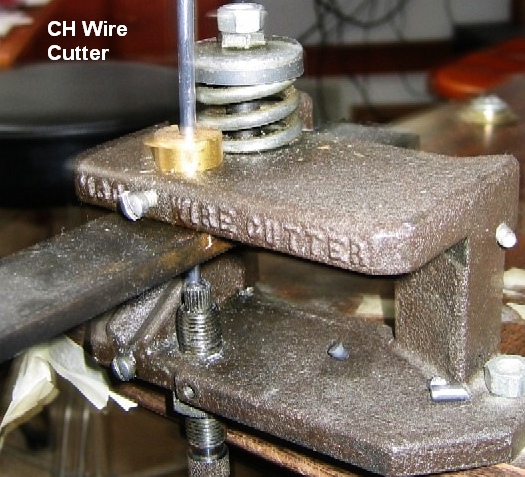
Share the post "Perfection at the Core — Bullet Making Tips from BIB Bullets"