|
March 30th, 2015
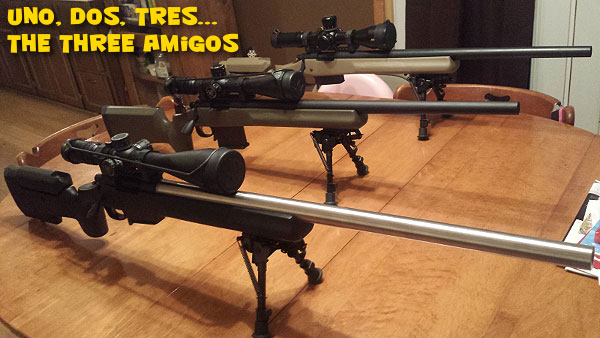
Jerod’s Tactical Trio
Many guys are lucky to have just one accurate tactical rifle fitted with a custom barrel and high-end optics. Well forum member Jerod (aka Stinnett1981) has three!
Jerod calls his tactical trio the “Three Amigos”. All are built with Manners Composite stocks and Bartlein barrels. But there are three different chamberings. In order below (from top to bottom) are: .308 Win (Bartlein 5R, 1:10″ twist); .223 Rem (Bartlein 5R, 1:8″ twist);,and 6.5×47 Lapua (Bartlein 5R 1:8.5″ twist). Read on for a full description of each build.
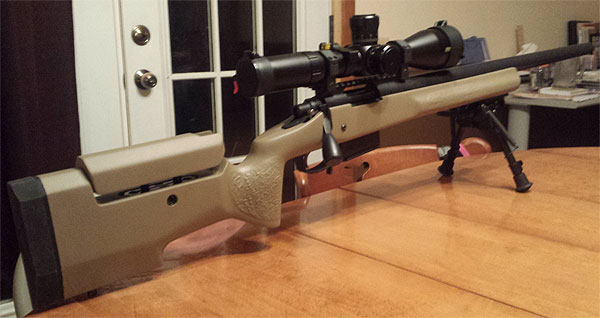
The tan rifle is Jerod’s .308 Winchester. It has a Manners T4A stock, trued Rem 700 SA, Badger M5 DBM, and Bartlein 5R 10-twist HV contour finished at 23″. The optic is a Bushnell XRS 4.5-30X50mm FFP with G2 reticle scope.
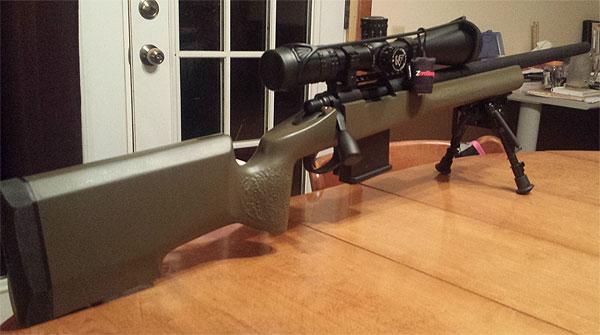
The Green rifle is a .223 Remington. This has a Manners T4 stock, trued Rem 700 SA, Badger M5 DBM, and Bartlein 5R 8-twist HV contour finished at 23″. On top is a Nightforce NXS F1 3.5-15X50mm FFP with MLR 2.0 reticle scope. Jerod says: “This scope and reticle are awesome.”
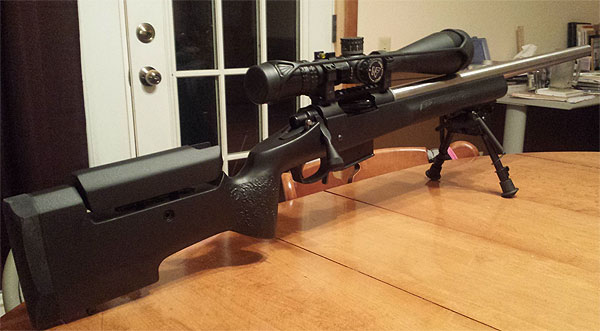
The Black rifle is chambered for the 6.5-47 Lapua. Components are: Manners T4A stock, Stiller TAC 30, Badger M5 DBM, Bartlein 5R 8.5-twist bull barrel (1″ at muzzle) finished at 26″. The scope is a Nightforce NXS 8-32X56mm with NP2DD reticle.
Share the post "Los Tacticales — The Three Amigos"
November 16th, 2014
Forum Member Chuck L. (aka “Ridgeway”) has created a handsome duo of 6mm Dashers for competitive benchrest and varmint matches in Pennsylvania. Both guns are built on Kelbly Panda RBLP actions, with Bartlein 8-twist barrels, and Shehane Laminated Tracker Stocks. However, the two rifles are not exact twins, as you can see. One, which we’ll call the Big Dasher, is built on a Shehane ST1000 Tracker stock. The other gun, the Small Dasher, sports Shehane’s “Baby Tracker” stock — a design used with great success by Richard Schatz. The Big Dasher, optimized for 1000-yard competition, also has a slightly longer freebore — 0.136″ vs. 0.104″ for the Small Dasher.
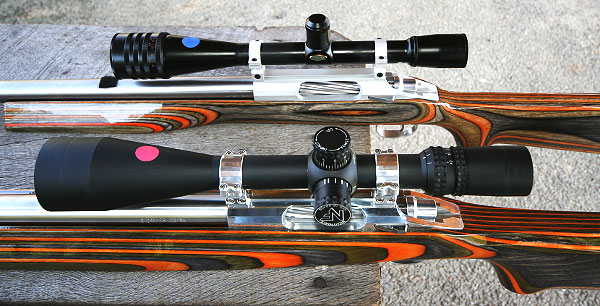
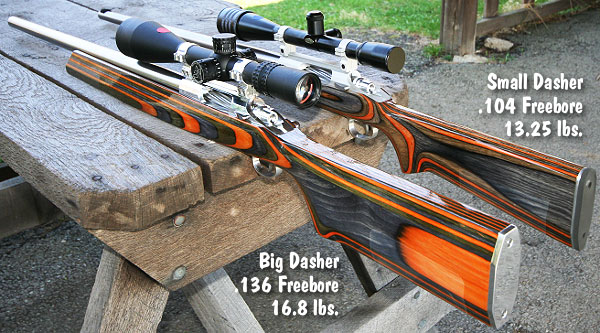

Chuck tells us: “I don’t get out shooting competition as much as I want due to time and family, but when I do compete, I shoot a Groundhog match at Southfork Rifle Club in Beaverdale, PA. Info on Southfork Club events can be found at Southforkrifleclub.com. The Southfork match is basically a 100-, 300- and 500-yard match with one sighter the entire match and 5 shots at each yardage for score. The Small Dasher, with the shorter ‘Baby Tracker’ stock, was set up for the Southfork Rifle Club’s ‘Light Unlimited’ class which has a 13.5-lb max weight.” (Editor: ‘unlimited’ is a misnomer for a weight-limited category.)
Chuck adds: “The Big Dasher with the heavy ST-1000 stock is set up for 1000-yard benchrest matches in Light Gun class. I hope to shoot a couple 1K matches with it at Reade Range in southwest Pennsylvania. I am still in load development for this rifle since it was just finished in January. One ironic thing is, it shoots the same load I’m shooting out of the lighter gun rather well. The only difference between the two chambers is the freebore is roughly thirty thousandths longer on the 1K gun (Large Dasher). I will also shoot this at Southfork in the ‘Heavy Unlimited’ class.”
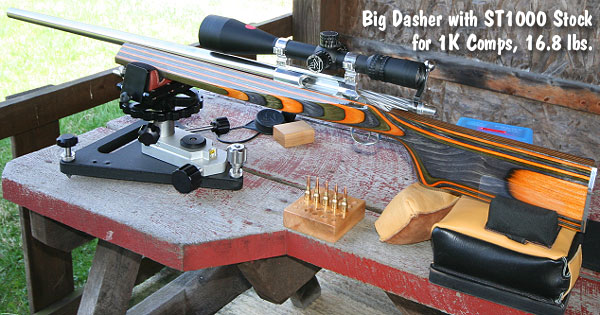
Specifications for the Dasher Duo:
Small Dasher (13.5-pounder): Chambered for 6mm Dasher with approximately .104 freebore and a .264 NK. (No way of knowing exactly since it freebore was done in a separate operation by Kelbly.) Components are: Shehane Baby Tracker stock, Kelbly Panda RPLB action, Bartlein 1:8″ LV barrel at 26 ¾”, Kelbly Rings, Weaver T36, Jewell trigger. The barrel was chambered by Kelblys and the stock was bedded, glued and balanced by a shooting buddy (Forum Member johara1). I clear-coated the stock with auto urethane. Total weight is 13 lbs., 4 ounces.
Big Dasher (1K Light Gun, 17-pounder): Chambered for 6mm Dasher with a .136 freebore and .264 neck (PTG Reamer). Components are: Shehane ST-1000 stock, Kelbly Panda RPLB action, Bartlein 1:8″ HV 5R barrel at 28″, Shehane +20-MOA rings, Nightforce NXS 12-42x56mm, Jewell trigger. The barrel work, pillar installation, and bedding was done by Dave Bruno. The stock was clear-coated by Chuck with auto urethane. Chuck also made the rear butt plate and balanced the rifle. Total weight: 16 lbs., 13 ounces. |
Dasher Case-Forming: Neck-Turn then Fire-form with Bullets Hard in Lands
To fireform, I turn my cases down to fit the chamber and stop where the false shoulder makes snug contact with the chamber. Fire-forming rounds are loaded up with a 29-grain charge of H4895 or Varget and a 108gr Berger bullet seated hard into the lands about 0.020″ past initial contact with the rifling. It takes about three firings to make a nice clean Dasher case with a sharp shoulder. I anneal about every 3-4 firings. I have many cases that have about 10+ firings on them and they are still shooting well. The primer pockets are a little looser, but still hold a primer.
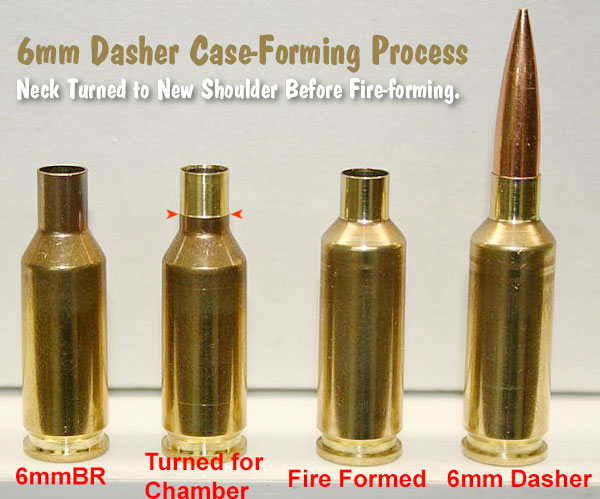
Both Dashers Group in the Ones at 100 Yards
My main bullet for both rifles is the 107gr Sierra MK, loaded with Reloder 15 powder, Lapua cases and CCI 450 primers. My main load for the Small Dasher is 33.0 grains of Reloder 15. This load shoots in the ones at 100 yards. For the Big Dasher, I’m still working on a load, although the same 33.0 grain load shoots in the ones in the heavier gun as well. I’m still looking for more velocity and my ‘max’ node. So far, I’ve gone well above 33.0 grains of RL 15 without pressure signs, but that load produces vertical at 100 yards, so I’m going to tinker with the load until I see pressure or it starts to shoot.
Share the post "Chuck’s Dazzling Dasher Duo — A Pair of Beauties"
August 16th, 2014
“Gain-twist” refers to a form of barrel rifling where the twist rate gets tighter over the length of the barrel. For example, a gain twist barrel might start with 1:12″ twist and finish with 1:8″ twist. There is some evidence that gain-twist rifling can deliver more velocity (compared to a conventional barrel) with certain cartridge types. There have also been claims of increased accuracy with some types of bullets, but such claims are more difficult to quantify.
Gain-twist rifling is not new. This form of rifling has been around for a long, long time. The first gain-twist barrels appeared in the late 1800s. However, in the last few years, there has been increased interest in gain-twist barrels for both short-range and long-range competition.
Video Explains Gain Twist Rifling
Radical Extreme Gain Twist Barrel Design
In this video from our friend John M. Buol Jr., gunsmith John Carlos talks about a fairly radical gain-twist barrel design for high power and service rifle shooters. Produced by Bartlein Barrels, this gain-twist barrel starts with a 1:14″ twist and finishes with a 1:6.8″ twist at the muzzle (See 1:50 time-mark). Carlos believes that this type of barrel delivers higher velocities while providing excellent accuracy for a wide range of bullet weights. In .223 caliber, the gain twist works with the 75-77 grain bullets used on the “short course” while also delivering excellent accuracy with the longer 80-90gr bullets used at 600 yards and beyond. Velocity is the important bonus for long-range use. Carlos says the gain twist barrels deliver greater muzzle velocity, allowing a 90 grain bullet to stay well above the transonic zone, even at 1000 yards. (See 4:50 time-mark.)
This 1:14″ to 1:6.8″ gain-twist barrel is the product of much experimentation by Carlos and Bartlein. Carlos states: “We’ve varied all sorts of internal dimensions, such as the land height, and the groove depth. We’ve tried 5R rifling and 4-groove rifling, and we’ve worked with various rates of twist, and I believe we have it down really well right now.”
In this video, John Carlos explains the history of gain-twist rifling, and he explains how modern Bartlein gain twist barrels have been developed in recent years for both benchrest and High Power applications. If you are interested in barrel technology and design, take the time to watch.
Erik Dahlberg illustration courtesy FireArmsID.com.
Share the post "Radical Gain-Twist Barrel for AR and High Power Rifles"
August 2nd, 2014
Brux Barrels, based in Lodi, Wisconsin, has earned a reputation for producing great-shooting tubes. Brux-made barrels have won their fair share of matches, and set some notable records in the process. Last year, Rodney Wagner shot the smallest five-shot, 600-yard group (.0349″) in the history of rifle competition, using a Brux barrel chambered for the 6mm Dasher.
Folks often ask us why Brux barrels shoot so well. “What’s the secret?” they ask. We can only answer with what Brux explains on its own website: “To make a cut-rifled barrel you have to start off with the proper ingredients: the best steel available, skill, and experience. Since there are really only two main suppliers of barrel-quality steel, the skill and experience is what really makes a barrel maker stand out.” Here is how Brux’s co-owners, Norman Brux and Ken Liebetrau, explain all the procedures involved in making a Brux cut-rifled barrel:
Brux Barrel-Making Process, Start to Finish
We start out with either 4150 chrome-moly or 416R stainless steel double stress-relieved bar stock. The bar stock starts out at 1-9/32″ in diameter and 20-24 feet long so we cut it to length.
Step two is to rough-contour the outside of the barrel blank in a lathe.
Thirdly, the blank gets mounted into a Barnes gun drill. The cutter bit has holes through which oil or coolant is injected under pressure to allow the evacuation of chips formed during the cutting process. This is called “oil-through” or “coolant-through”. Without this, you wouldn’t want to even attempt drilling a hole 30” long and under ¼” in diameter. The combination of a 3600rpm and good flushing allows us to drill a beautifully straight and centered hole .005” under “land” diameter at a rate of 1” per minute.
Clean the barrel.
Next the blank is sent back to the lathe to machine the finished contour of the outside.
Clean the barrel again.
Now, the blank is sent on to the Pratt & Whitney reamer in which an “oil through” reaming tool is used to cut away the extra .005” left in the drilling process. The reamer makes an extremely accurate bore size and after it is finished the bore will have a better surface finish and will be at the proper “land” diameter.
Clean the barrel again.
In the sixth step we hand lap each barrel to remove any slight tool marks that may have been left by the reamer and inspect every one with a bore scope. If the barrel doesn’t meet our standards for surface finish and tolerance it doesn’t get any further.
Clean the barrel again.
The barrels then go onto the rifling machine which is responsible for cutting the all so familiar grooves in the bore. A caliber/land configuration-specific rifling head is used to progressively shave away small amounts of steel to form the rifling grooves. This is accomplished by simultaneously pulling the rifling head through the reamed blank as the blank is spun at a controlled rate. After each cut, the blank is rotated 90 degrees (for a four-land configuration) and after one full rotation (360 degrees) the rifling head is slightly raised to shave off the next bit of material. This process is repeated until we reach groove diameter.
Clean the barrel again.
Lastly, the barrel is hand-lapped again (to ensure a smooth bore), and a final inspection is performed with the bore scope.
The barrel is cleaned one last time, wrapped, packed, and shipped to [the customer]. |
Anyone reading this detailed description of the Brux barrel-making process will doubtless come away with a new appreciation for the time, effort, and dedication required to produce a premium match-grade cut-rifled barrel. Obviously, there are no easy shortcuts and great attention to detail is required each step of the way. As shooters we’re lucky that we have barrel-makers so dedicated to their craft.
Credit James Mock for steering us to this Barrel Making 101 feature on the Brux website.
Share the post "How Brux Barrels are Made — Precision Start to Finish"
April 24th, 2013
This story first appeared last year. We’re featuring it again by popular request.
Some of our mechanically-skilled readers chamber their own barrels or bed their own stocks. But these are relatively simple tasks compared to the jobs of constructing an entire rifle plus building an advanced front rest from scratch. Well that’s exactly what Forum member Steve B. (aka Essexboy) did. He built his own rifle and an impressive twin-belt-drive pedestal rest. (Click photo below to see large version). And get this, Steve’s home-made rifle was victorious in its first-ever match. Steve reports: “I shot my first Comp with the rifle this weekend and managed to win with a score of 239-21!” (The match was shot at 300/500/600/1000/1100 with English scoring of 5 points for center bullseye).
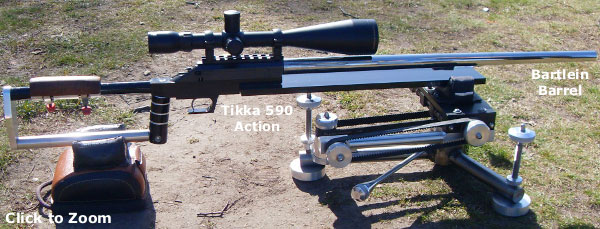

Do-It-Yourself F-Open Rig from England
Steve, who hails from Essex in the UK, constructed virtually every component of his skeleton-style rifle except the 28″ HV Bartlein barrel (chambered as a 6mm Dasher) and the Tikka 590 donor action. Steve also did all the design and fabrication work on his one-of-a-kind front rest. Steve tells us: “Over the last year or so, I made this rifle stock and rest. I managed to make it all on a little Myford Lathe, as you can tell I’m no machinist but it saved me a load of money — so far I’ve got about $200 invested plus the barrelled action. The stock is aluminum except for the stainless steel bag runner. The rifle came in at one ounce under weight limit for F-Class Open division.” Steve did get help with the chambering and barrel-fitting, but he hopes to do all the barrel work himself on his next project.
The gun is very accurate. Steve notes: “I have shot the rifle to 1100 yards and it shoots well. Last time out the rifle dropped just one point at 1000 yards and 5 points at 1100 yards [English scoring system]. I know it’s not pretty, but it got me shooting long range F-Class for peanuts.” Message to Steve: Don’t worry how it looks. As another Forum member observed: “Any rifle that shoots well at 1100 yards is beautiful….”
Steve started with a Tikka 590 action: “The whole stock was made on a small (6.5×13) lathe and a vertical slide. This caused a few head scratching moments, figuring out how to hold the T6/HE30 alloy for the milling/turning operations, but it did teach me a few things. The hardest parts were clamping the longer sections (such as the fore-end) and keeping it all square. Due to the short cross-slide travel I had to keep re-setting the parts. I managed to keep all measurements to .0001″ (one thousandth). I’m most proud of the trigger guard (photo below). This took a full day but came out really well, even if I say so myself.”
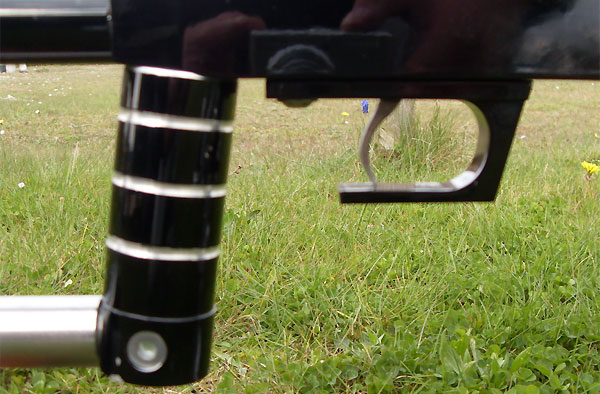
Belt-Driven Front Rest
We’re impressed with Steve’s ingenious front rest. Steve explains: “The rest is belt-driven and still in the experimental stage — hence no powder coating or polishing yet. I may have gone over the top as the key moving parts (the pulleys) run on three (3) types of bearings: radial; reamed bush; and a ball race. The main post runs on a radial bearing and the feet even have bearings in them, so when I raise the main body up (for rough height adjustment) the foot stays static.”
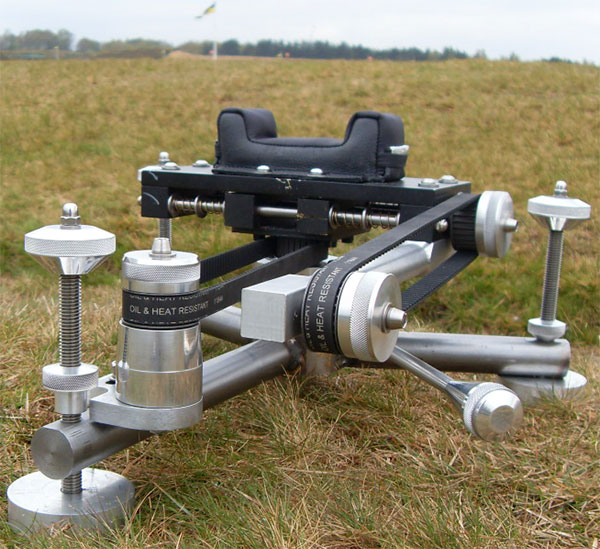
Will Steve build another rifle? Steve says he will, and he’s upgraded his tools: “Since building the rifle I have acquired a bigger lathe (Harrison m250) and a milling machine. For the next project I hope to be able to do the barrel work (threading, chambering, crowning) as well.” The next gun might be another Dasher. Steve explains: “After extensive reading on AccurateShooter.com, I chose the 6mm Dasher chambering, as I have a shoulder problem and can’t shoot a rifle with a lot of recoil.”
Share the post "Forum Member Builds DIY F-Class Rifle and Belt-Drive Rest"
April 11th, 2012
After we ran our Bulletin news item about Ron Boyd’s amazing 1.462″ 5-shot group at 1000 yards, many readers wanted to see some close-up photos of Ron’s rig. Thanks to Robert Ross of the MidWest Benchrest Club, we have some photos of Ron with his ultra-accurate 6mm Dasher 17-lb Light Gun. This rifle features a BAT SV action, Precision Rifle & Tool (PR&T) “Hammerhead stock” with 5″-wide front wings, Nightforce 12-42 Benchrest scope, and Jewell trigger. Ron had just added a 30″ 1:8″-twist Bartlein barrel to the gun before shooting the 1.462″ group. That barrel only had about 40 rounds through it when it produced the near-record group. The barrel in photos below was a 28″ Benchmark, recently replaced with the new Bartlein. Ron’s ultra-accurate 6 Dasher load consists of surplus Long Range Match powder, with Spencer 103gr bullets. Ron also anneals his Dasher brass after every firing.
CLICK Small gallery photos to view full-size images
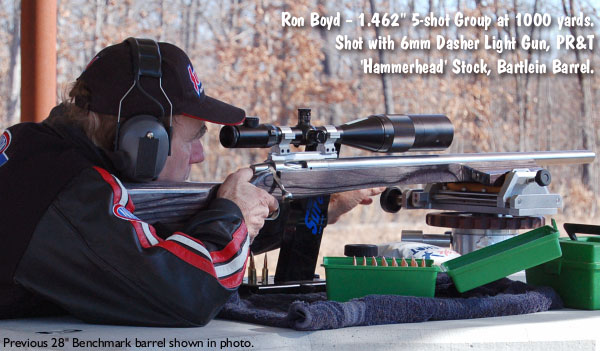
Henry Pasquet’s .284 Win Heavy Gun
At the same Midwest Benchrest Club IBS match where Ron shot his small five-shot group, Henry Pasquet drilled a very impressive 3.348″ ten-shot group. This group was just .304″ off the IBS 10-shot Heavy Gun record of 3.044″ shot by Joel Pendergraft in 2009. We are told that Henry was running a straight .284 Winchester. You can see in the inset photos below that Henry uses a tuner on his barrel. He also has fitted an extra-wide front sled and a machined rear “keel” to reduce torque and improve tracking. Henry can adjust windage and elevation with BOTH his Fulghum front rest (from Randolph Machine) and his adjustable rear rest.
CLICK Small gallery photos to view full-size images
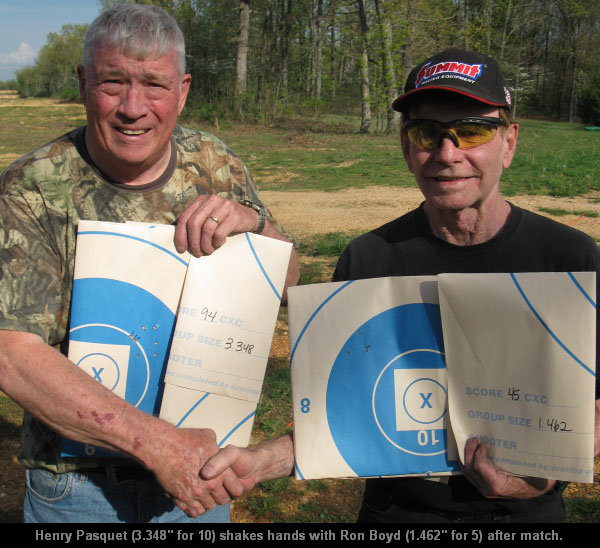
Share the post "Spotlight: Ron Boyd’s Light Gun and Henry Pasquet’s Heavy Gun"
|