|
December 30th, 2024
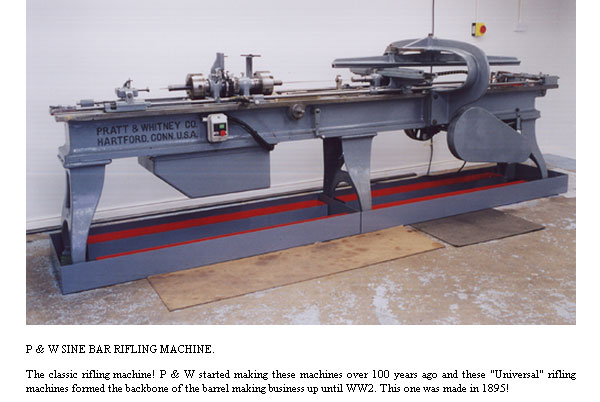
You’ve probably heard of cut-rifling, but did you know this process was invented in Germany nearly 500 years ago? Read on to learn more about how a cut-rifled barrel is made…
The cut-rifling process, used by leading barrel-makers such as Bartlein, Blake, Brux, and Krieger can yield a very high-quality barrel with a long useful life. Cut-rifled barrels have been at the top in short- and long-range benchrest competition in recent years, and cut-rifled barrels have long been popular with F-Class and High Power shooters.
You may be surprised to learn that cut-rifling is probably the oldest method of rifling a barrel. Invented in Nuremberg around 1520, the cut-rifling technique creates spiral grooves in the barrel by removing steel using some form of cutter. In its traditional form, cut rifling may be described as a single-point cutting system using a “hook” cutter. The cutter rests in the cutter box, a hardened steel cylinder made so it will just fit the reamed barrel blank and which also contains the cutter raising mechanism.
Above is a computer animation of an older style, sine-bar cut-rifling machine. Some machine features have been simplified for the purposes of illustration, but the basic operation is correctly shown. No, the cut-rifling machines at Krieger don’t use a hand-crank, but the mechanical process shown in this video is very similar to the way cut-rifling is done with more modern machines.
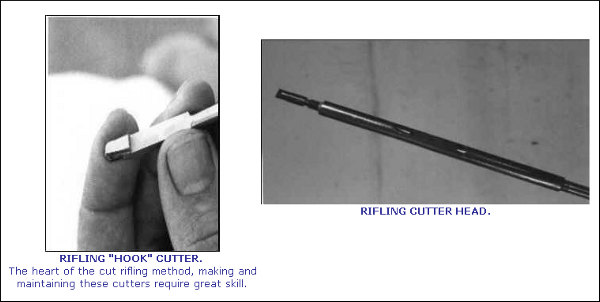
Read About Cut-Rifling Process at FirearmsID.com
To learn more about the barrel-making process, and cut-rifling in particular, visit FirearmsID.com. There you’ll find a “must-read” article by Dr. Geoffrey Kolbe: The Making of a Rifled Barrel. This article describes in detail how barrels are crafted, using both cut-rifling and button-rifling methods. Kolbe (past owner of Border Barrels) covers all the important processes: steel selection, hole drilling, hole reaming, and rifling (by various means). You’ll find a very extensive discussion of how rifling machines work. Here’s a short sample:
“At the start of World War Two, Pratt & Whitney developed a new, ‘B’ series of hydraulically-powered rifling machines, which were in fact two machines on the same bed. They weighed in at three tons and required the concrete floors now generally seen in workshops by this time. About two thousand were built to satisfy the new demand for rifle barrels, but many were broken up after the war or sold to emerging third world countries building up their own arms industry.
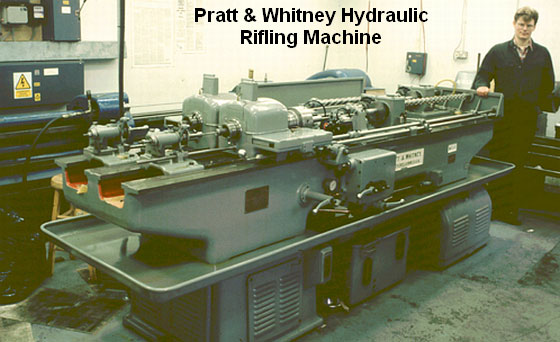
Very few of these hydraulic machines subsequently became available on the surplus market and now it is these machines which are sought after and used by barrel makers like John Krieger and ‘Boots’ Obermeyer. In fact, there are probably less of the ‘B’ series hydraulic riflers around today than of the older ‘Sine Bar’ universal riflers.
The techniques of cut rifling have not stood still since the end of the war though. Largely due to the efforts of Boots Obermeyer the design, manufacture and maintenance of the hook cutter and the cutter box have been refined and developed so that barrels of superb accuracy have come from his shop. Cut rifled barrel makers like John Krieger (Krieger Barrels), Mark Chanlyn (Rocky Mountain Rifle Works) and Cliff Labounty (Labounty Precision Reboring)… learned much of their art from Boots Obermeyer, as did I.” — Geoffrey Kolbe
Video find by Boyd Allen. Archive photos from Border Barrels in the UK.
Share the post "How Cut-Rifled Barrels Are Made — History of Cut-Rifling Process"
December 16th, 2022
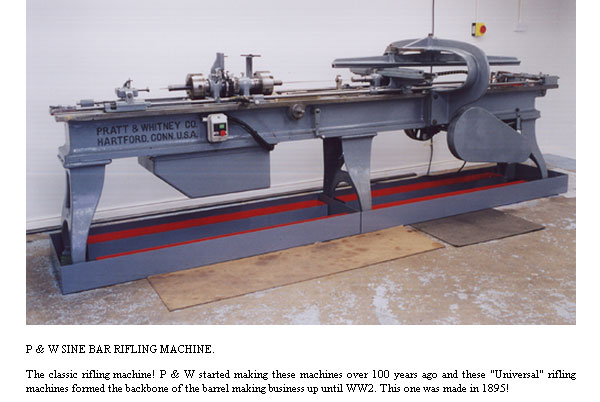
You’ve probably heard of cut-rifling, but did you know this process was invented in Germany nearly 500 years ago? Read on to learn more about how a cut-rifled barrel is made…
The cut-rifling process, used by leading barrel-makers such as Bartlein, Blake, Brux, and Krieger can yield a very high-quality barrel with a long useful life. Cut-rifled barrels have been at the top in short- and long-range benchrest competition in recent years, and cut-rifled barrels have long been popular with F-Class and High Power shooters.
You may be surprised to learn that cut-rifling is probably the oldest method of rifling a barrel. Invented in Nuremberg around 1520, the cut-rifling technique creates spiral grooves in the barrel by removing steel using some form of cutter. In its traditional form, cut rifling may be described as a single-point cutting system using a “hook” cutter. The cutter rests in the cutter box, a hardened steel cylinder made so it will just fit the reamed barrel blank and which also contains the cutter raising mechanism.
Above is a computer animation of an older style, sine-bar cut-rifling machine. Some machine features have been simplified for the purposes of illustration, but the basic operation is correctly shown. No, the cut-rifling machines at Krieger don’t use a hand-crank, but the mechanical process shown in this video is very similar to the way cut-rifling is done with more modern machines.
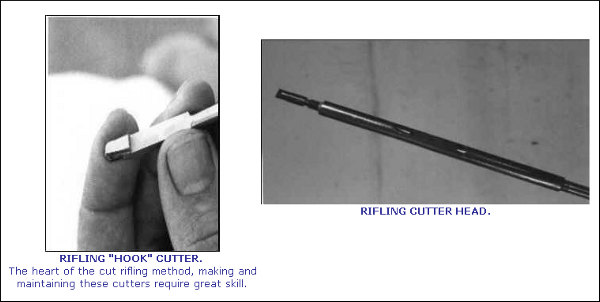
Read About Cut-Rifling Process at FirearmsID.com
To learn more about the barrel-making process, and cut-rifling in particular, visit FirearmsID.com. There you’ll find a “must-read” article by Dr. Geoffrey Kolbe: The Making of a Rifled Barrel. This article describes in detail how barrels are crafted, using both cut-rifling and button-rifling methods. Kolbe (past owner of Border Barrels) covers all the important processes: steel selection, hole drilling, hole reaming, and rifling (by various means). You’ll find a very extensive discussion of how rifling machines work. Here’s a short sample:
“At the start of World War Two, Pratt & Whitney developed a new, ‘B’ series of hydraulically-powered rifling machines, which were in fact two machines on the same bed. They weighed in at three tons and required the concrete floors now generally seen in workshops by this time. About two thousand were built to satisfy the new demand for rifle barrels, but many were broken up after the war or sold to emerging third world countries building up their own arms industry.
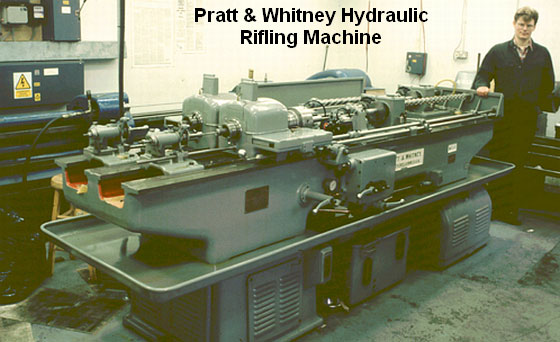
Very few of these hydraulic machines subsequently became available on the surplus market and now it is these machines which are sought after and used by barrel makers like John Krieger and ‘Boots’ Obermeyer. In fact, there are probably less of the ‘B’ series hydraulic riflers around today than of the older ‘Sine Bar’ universal riflers.
The techniques of cut rifling have not stood still since the end of the war though. Largely due to the efforts of Boots Obermeyer the design, manufacture and maintenance of the hook cutter and the cutter box have been refined and developed so that barrels of superb accuracy have come from his shop. Cut rifled barrel makers like John Krieger (Krieger Barrels), Mark Chanlyn (Rocky Mountain Rifle Works) and Cliff Labounty (Labounty Precision Reboring)… learned much of their art from Boots Obermeyer, as did I.” — Geoffrey Kolbe
Video find by Boyd Allen. Archive photos from Border Barrels. In June 2013, Birmingham Gunmakers Ltd. acquired Border Barrels. Dr. Geoffrey Kolbe has set up a new company called BBT Ltd. which produces chamber reamers and other gunsmithing tools and gauges. (Thanks to L. Holland for the Kolbe update).
Share the post "How Cut-Rifled Barrels Are Made — History of Cut-Rifling Process"
December 4th, 2020
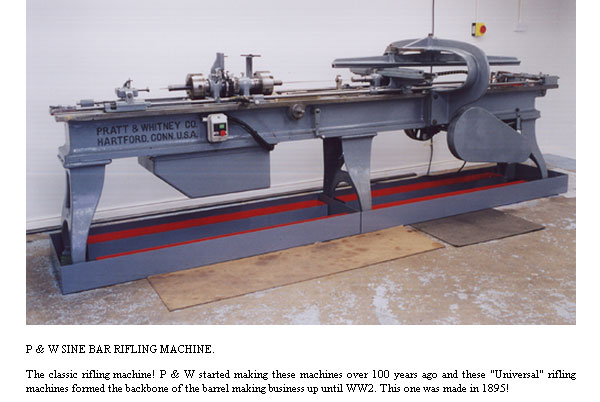
You’ve probably heard of cut-rifling, but did you know this process was invented in Germany nearly 500 years ago? Read on to learn more about how a cut-rifled barrel is made…
The cut-rifling process, used by leading barrel-makers such as Bartlein, Blake, Brux, Krieger, and Obermeyer, can yield a very high-quality barrel with a long useful life. Cut-rifled barrels have been at the top in short- and long-range benchrest competition in recent years, and cut-rifled barrels have long been popular with F-Class and High Power shooters.
You may be surprised to learn that cut-rifling is probably the oldest method of rifling a barrel. Invented in Nuremberg around 1520, the cut-rifling technique creates spiral grooves in the barrel by removing steel using some form of cutter. In its traditional form, cut rifling may be described as a single-point cutting system using a “hook” cutter. The cutter rests in the cutter box, a hardened steel cylinder made so it will just fit the reamed barrel blank and which also contains the cutter raising mechanism.
Above is a computer animation of an older style, sine-bar cut-rifling machine. Some machine features have been simplified for the purposes of illustration, but the basic operation is correctly shown. No, the cut-rifling machines at Krieger don’t use a hand-crank, but the mechanical process shown in this video is very similar to the way cut-rifling is done with more modern machines.
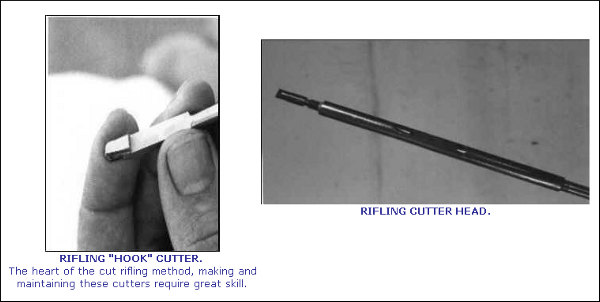
Read About Cut-Rifling Process at FirearmsID.com
To learn more about the barrel-making process, and cut-rifling in particular, visit FirearmsID.com. There you’ll find a “must-read” article by Dr. Geoffrey Kolbe: The Making of a Rifled Barrel. This article describes in detail how barrels are crafted, using both cut-rifling and button-rifling methods. Kolbe (past owner of Border Barrels) covers all the important processes: steel selection, hole drilling, hole reaming, and rifling (by various means). You’ll find a very extensive discussion of how rifling machines work. Here’s a short sample:
“At the start of World War Two, Pratt & Whitney developed a new, ‘B’ series of hydraulically-powered rifling machines, which were in fact two machines on the same bed. They weighed in at three tons and required the concrete floors now generally seen in workshops by this time. About two thousand were built to satisfy the new demand for rifle barrels, but many were broken up after the war or sold to emerging third world countries building up their own arms industry.
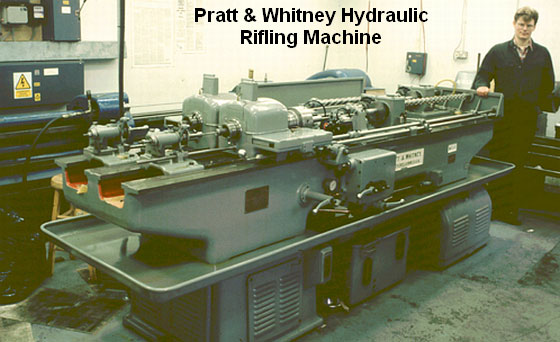
Very few of these hydraulic machines subsequently became available on the surplus market and now it is these machines which are sought after and used by barrel makers like John Krieger and ‘Boots’ Obermeyer. In fact, there are probably less of the ‘B’ series hydraulic riflers around today than of the older ‘Sine Bar’ universal riflers.
The techniques of cut rifling have not stood still since the end of the war though. Largely due to the efforts of Boots Obermeyer the design, manufacture and maintenance of the hook cutter and the cutter box have been refined and developed so that barrels of superb accuracy have come from his shop. Cut rifled barrel makers like John Krieger (Krieger Barrels), Mark Chanlyn (Rocky Mountain Rifle Works) and Cliff Labounty (Labounty Precision Reboring)… learned much of their art from Boots Obermeyer, as did I.” — Geoffrey Kolbe
Video find by Boyd Allen. Archive photos from Border Barrels. In June 2013, Birmingham Gunmakers Ltd. acquired Border Barrels. Dr. Geoffrey Kolbe has set up a new company called BBT Ltd. which produces chamber reamers and other gunsmithing tools and gauges. (Thanks to L. Holland for the Kolbe update).
Share the post "Cut-Rifled Barrels — History of the Cut-Rifling Process"
December 17th, 2016
Brux Barrels, based in Lodi, Wisconsin, has earned a reputation for producing great-shooting tubes. Brux-made barrels have won their fair share of matches, and set some notable records in the process. A few years back, Rodney Wagner shot the smallest five-shot, 600-yard group (0.336″) in the history of rifle competition, using a Brux barrel chambered for the 6mm Dasher.
Folks often ask us why Brux barrels shoot so well. “What’s the secret?” they ask. We can only answer with what Brux explains on its own website: “To make a cut-rifled barrel you have to start off with the proper ingredients: the best steel available, skill, and experience. Since there are really only two main suppliers of barrel-quality steel, the skill and experience is what really makes a barrel maker stand out.” Here is how Brux’s co-owners, Norman Brux and Ken Liebetrau, explain all the procedures involved in making a Brux cut-rifled barrel:
Brux Barrel-Making Process, Start to Finish
We start out with either 4150 chrome-moly or 416R stainless steel double stress-relieved bar stock. The bar stock starts out at 1-9/32″ in diameter and 20-24 feet long so we cut it to length.
Step two is to rough-contour the outside of the barrel blank in a lathe.
Thirdly, the blank gets mounted into a Barnes gun drill. The cutter bit has holes through which oil or coolant is injected under pressure to allow the evacuation of chips formed during the cutting process. This is called “oil-through” or “coolant-through”. Without this, you wouldn’t want to even attempt drilling a hole 30” long and under ¼” in diameter. The combination of a 3600rpm and good flushing allows us to drill a beautifully straight and centered hole .005” under “land” diameter at a rate of 1” per minute.
Clean the barrel.
Next the blank is sent back to the lathe to machine the finished contour of the outside.
Clean the barrel again.
Now, the blank is sent on to the Pratt & Whitney reamer in which an “oil through” reaming tool is used to cut away the extra .005” left in the drilling process. The reamer makes an extremely accurate bore size and after it is finished the bore will have a better surface finish and will be at the proper “land” diameter.
Clean the barrel again.
In the sixth step we hand lap each barrel to remove any slight tool marks that may have been left by the reamer and inspect every one with a bore scope. If the barrel doesn’t meet our standards for surface finish and tolerance it doesn’t get any further.
Clean the barrel again.
The barrels then go onto the rifling machine which is responsible for cutting the all so familiar grooves in the bore. A caliber/land configuration-specific rifling head is used to progressively shave away small amounts of steel to form the rifling grooves. This is accomplished by simultaneously pulling the rifling head through the reamed blank as the blank is spun at a controlled rate. After each cut, the blank is rotated 90 degrees (for a four-land configuration) and after one full rotation (360 degrees) the rifling head is slightly raised to shave off the next bit of material. This process is repeated until we reach groove diameter.
Clean the barrel again.
Lastly, the barrel is hand-lapped again (to ensure a smooth bore), and a final inspection is performed with the bore scope.
The barrel is cleaned one last time, wrapped, packed, and shipped to [the customer]. |
Anyone reading this detailed description of the Brux barrel-making process will doubtless come away with a new appreciation for the time, effort, and dedication required to produce a premium match-grade cut-rifled barrel. Obviously, there are no easy shortcuts and great attention to detail is required each step of the way. As shooters we’re lucky that we have barrel-makers so dedicated to their craft.
Credit James Mock for steering us to this Barrel Making 101 feature on the Brux website.
Share the post "How Brux Barrels Are Made — The Pursuit of Perfection"
June 1st, 2015
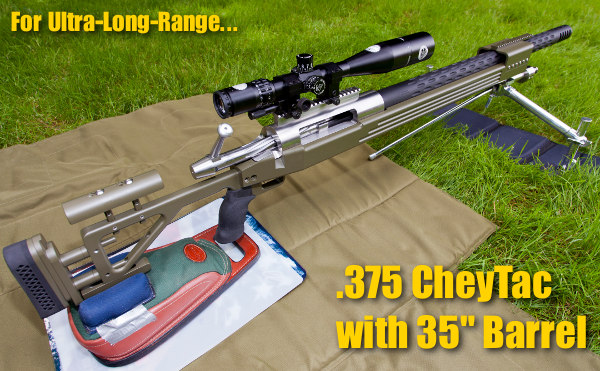
Click above image to view full-screen photo.
Our friend Darrell Buell has a new Beast — a monster 64-inch-long .375 CheyTac that weighs more than 70 pounds! Designed for ultra-long-range shooting (two miles and beyond), this beast represents the state-of-the-art in extreme long-range rifles.
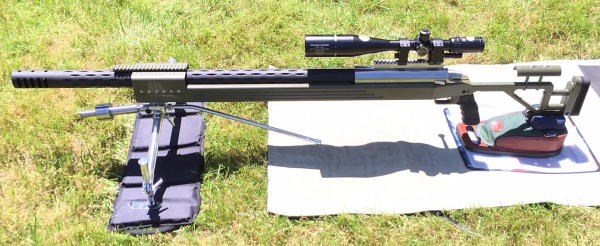
Darrell reports: “This rifle is pretty much purpose-built to shoot 2+ miles extremely accurately. It is a .375 CheyTac (lengthened) built on a BAT 2.5″ action. The custom 35″, 1:10″-twist Brux barrel is a fat, 2″-diameter ‘straight taper’ with fluting. A custom 5″-long muzzle brake is fitted at the end. All barreled action work was done by R.W. Snyder Custom Rifles. The stock was created to fit the build by PDC Custom, and the massive muzzle brake as well.” The “bridge” at the end may look like a barrel block, but it’s not — the barrel completely free-floats. (The Picatinny rail on top of the bridge allows use of an overhanging bipod as an alternative to the JoyPod).

Darrell has lots of elevation on tap: “With 150 MOA in the Ivey rings, another 20 MOA in the scope rail, 55 MOA in the Nightforce Competition scope, and 10 MOA in the FCR-1 reticle, there’s an impressive +235 MOA available.”
Share the post "Buell’s Beast: Heavy Artillery for ELR and 2-Mile Match"
September 18th, 2014
Have you ever wondered how a cut-rifled barrel is made? This process, used by leading barrel-makers such as Bartlein, Border, Brux, Krieger, and Obermeyer, can yield a very high-quality barrel with a long useful life. Cut-rifled barrels have been at the top in short- and long-range benchrest competition in recent years, and cut-rifled barrels have long been popular with F-Class and High Power shooters.
You may be surprised to learn that cut-rifling is probably the oldest method of rifling a barrel. Invented in Nuremberg around 1520, the cut-rifling technique creates spiral grooves in the barrel by removing steel using some form of cutter. In its traditional form, cut rifling may be described as a single-point cutting system using a “hook” cutter. The cutter rests in the cutter box, a hardened steel cylinder made so it will just fit the reamed barrel blank and which also contains the cutter raising mechanism.
Above is a computer animation of an older style, sine-bar cut-rifling machine. Some machine features have been simplified for the purposes of illustration, but the basic operation is correctly shown. No, the cut-rifling machines at Krieger don’t use a hand-crank, but the mechanical process shown in this video is very similar to the way cut-rifling is done with more modern machines.
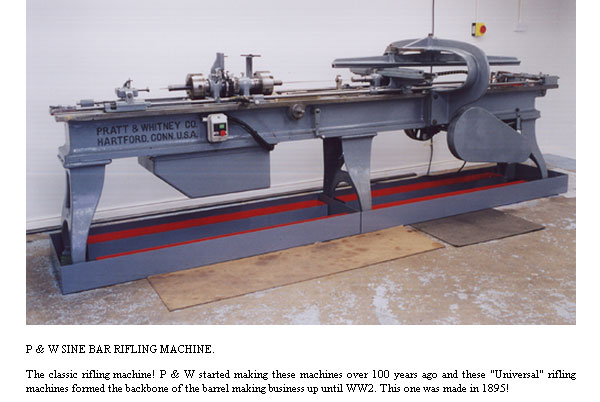
Read About Cut-Rifling Process at Border-Barrels.com
Read About Cut-Rifling Process at Border-Barrels.com
To learn more about the barrel-making process, and cut-rifling in particular, visit FirearmsID.com. There you’ll find a “must-read” article by Dr. Geoffrey Kolbe: The Making of a Rifled Barrel. This article describes in detail how barrels are crafted, using both cut-rifling and button-rifling methods. Kolbe (past owner of Border Barrels) covers all the important processes: steel selection, hole drilling, hole reaming, and rifling (by various means). You’ll find a very extensive discussion of how rifling machines work. Here’s a short sample:
“At the start of World War Two, Pratt & Whitney developed a new, ‘B’ series of hydraulically-powered rifling machines, which were in fact two machines on the same bed. They weighed in at three tons and required the concrete floors now generally seen in workshops by this time. About two thousand were built to satisfy the new demand for rifle barrels, but many were broken up after the war or sold to emerging third world countries building up their own arms industry.
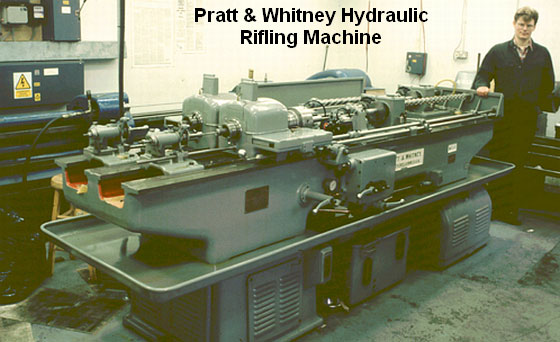
Very few of these hydraulic machines subsequently became available on the surplus market and now it is these machines which are sought after and used by barrel makers like John Krieger and ‘Boots’ Obermeyer. In fact, there are probably less of the ‘B’ series hydraulic riflers around today than of the older ‘Sine Bar’ universal riflers.
The techniques of cut rifling have not stood still since the end of the war though. Largely due to the efforts of Boots Obermeyer the design, manufacture and maintenance of the hook cutter and the cutter box have been refined and developed so that barrels of superb accuracy have come from his shop. Cut rifled barrel makers like John Krieger (Krieger Barrels), Mark Chanlyn (Rocky Mountain Rifle Works) and Cliff Labounty (Labounty Precision Reboring)… learned much of their art from Boots Obermeyer, as did I.” — Geoffrey Kolbe
Video find by Boyd Allen. Archive photos from Border-Barrels.com. In June 2013, Birmingham Gunmakers Ltd. acquired Border Barrels. Dr. Geoffrey Koble continues to work for Border Barrels, which maintains operations in Scotland.
Share the post "Video Animation Shows How the Cut-Rifling Process Works"
November 13th, 2013
Steven Blair’s recent report on the .300 WSM for F-Class stirred quite a bit of interest. If you’re a serious F-Open competitor, you’ll definitely want to read that article, which covers the pros and cons of the .30-Cal WSM loaded with the ultra-high-BC 230gr Berger Hybrid bullets.
If you’re thinking about building a .300 WSM for F-Class, here’s a rig that can give you some design and hardware ideas. This eye-catching custom .300 WSM F-Open rig belongs to Forum member Keith T. (aka “KT”). With its striking “bumblebee” color scheme, it will certainly get noticed on the firing line.
Click Photos to see full-screen versions.
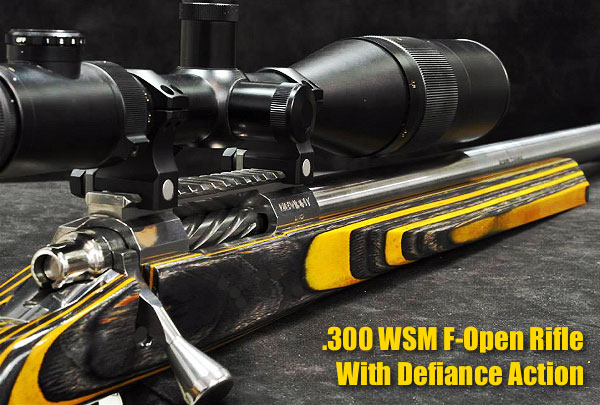
Bold Bumblebee .300 WSM for F-Class
Forum member Keith T. (aka “KT”) just got his hands on his new .300 WSM for F-Class and long-range competition. It’s a handsome brute, decked out in a “bumblebee” (yellow and black) laminated stock. Keith’s rifle features a Defiance Machine Deviant Long Magnum action (with Jewell trigger) in a Precision Rifle & Tool (PR&T) F-Class Lowboy stock. Keith has two 30″-long, 1:9″-twist barrels for the gun, one made by Brux Barrels, and the other by Bartlein. Both barrels have identical .300 WSM chambers cut with the same reamer. Keith will test both and then use the best-performing of the two in competition. Riding on top is a Nightforce 12-42x56mm Benchrest Model scope. All the work was done by Accurate Ordnance (AO), based in Winder, Georgia.
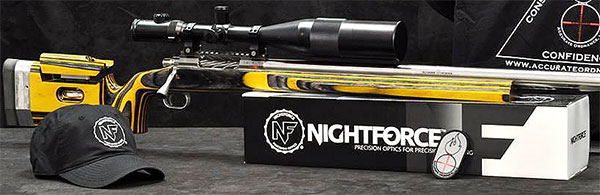
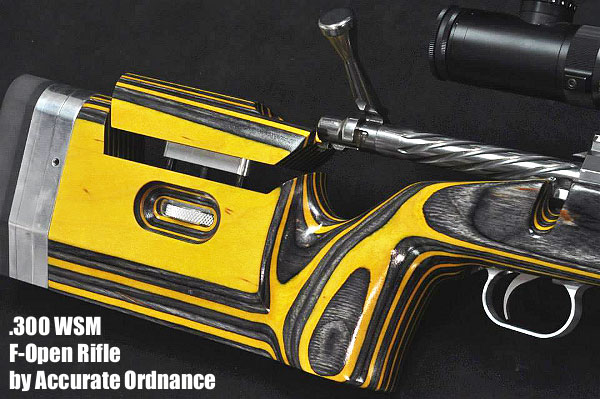
Keith reports: “This one took a while to get built due to parts availability issues, but I’m glad it’s done! Thanks to Accurate Ordnance and Nightforce and all their help.” NOTE: Accurate Ordnance tells us that a rifle like this can normally be completed in 6-8 weeks, once all key parts are in hand.
Share the post "Bumblebee .300 WSM F-Open Rig with Defiance ‘Deviant’ Action"
July 1st, 2009
Kudos to Forum Member John Dunbar (aka JD12)! Just this past weekend John won the Wisconsin State F-Class championship shooting a “home-built” .284 Winchester with a Savage target action. John designed and fabricated the aluminum stock himself. It features a central barrel block clamping a 32″ Brux barrel. Get this — John completed the rifle only 5 days before the match: “I finished machining/assembly on Monday night, did load workup Wednesday and Thursday nights, loaded rounds Friday night, and headed to Lodi at 4:30 on Saturday morning.” John also made his own co-axial front rest. He reports: “The rest worked really well this past weekend but as always there’s some small tweeking to do.”
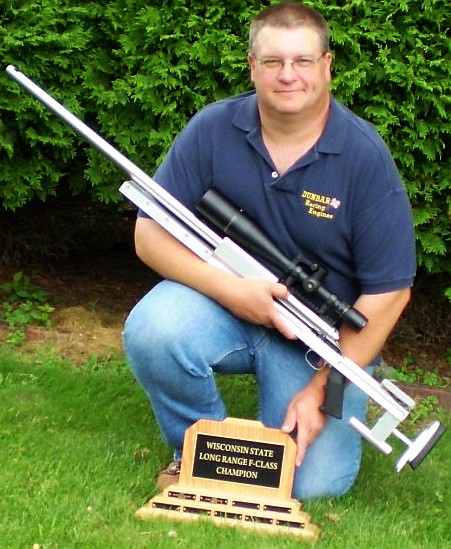
John tells us: “I want to thank Jim See from Center Shot Rifles. He did the barrel chambering and installation and action work — he does excellent work. I also want to thank Ken and Norm from Brux Barrels. Their barrels shoot — no questions asked.”
The rifle is chambered as a straight (non-improved) .284 Winchester, with 32″ barrel. At the match, John shot 180gr Bergers pushed by a stout load of Hodgdon 4831sc. John notes: “Most of the experienced shooters at Lodi, WI told me when barrel gets a few hundred rounds through it, I may have to drop the powder back as they found the barrel might speed up. The gun only had about 80 rounds of development loads through it before [the Championship match at Lodi]. I have some RE17 sitting here to try but now i’m thinking why screw with something that’s working!”
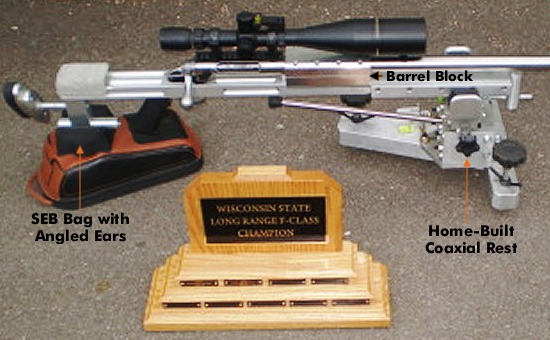
John’s rig features a Savage target action (with factory Accutrigger) trued up by Jim at Center Shot Rifles. On top is a Sightron SIII 8×32-56 scope (Hey we told you they were good). Take a look at the rear bag in the above photo. Notice that the ears are set off-axis? John explains: “The rear bag is a SEB from Ernie in Gillette, WY. It has the twisted ears on it so you can rest your hand right along side of stock. I really like it this way — it’s very comfortable.”
Share the post "F-Classer Wins State Title with Home-Built Savage"
|