Lothar Walther UltraLight Barrels — Less Heat, Half the Weight
We’re excited when major barrel-makers offer new technologies that promise worthwhile performance benefits for hunters or match shooters. Lothar Walther (LW) has developed a new bi-metal barrel system that cuts weight dramatically while promising significantly-enhanced heat dissipation.
Walther’s new Ultra-Lightweight Barrels combine steel with lightweight alloys. This results in a significant weight reduction without the use of carbon fiber, epoxy binders, or other heat-retaining materials. Beginning as an LW50 stainless blank, the barrel is precision-machined to remove excess weight. An outer casing of light-weight alloys is machined and the two are fitted together without adhesives. Basically you end up with the steel inner barrel inside a larger-diameter fluted aluminum outer barrel (see diagram). This gives you the ‘best of both worlds’ — light weight for ease of carry, and thick diameter for rigidity and enhanced heat dissipation. Near the action, the barrel remains all-steel.
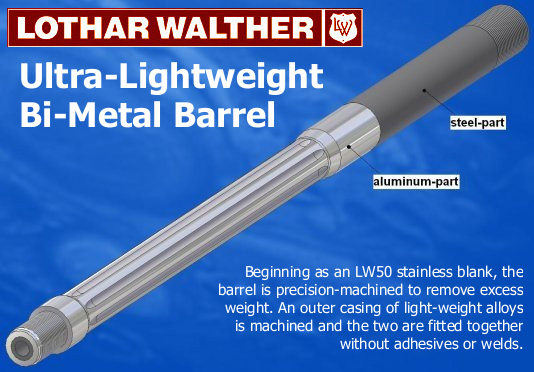
We haven’t tested one of these bi-metal composite barrels, but the potential for significant weight savings is obvious — aluminum is a lot lighter than steel. What’s more, a metals expert we contacted said that a bi-metal system employing fluted aluminum over steel, if assembled properly, could dissipate heat much better than steel alone (given the same diameter). Stainless steel has a thermal conductivity factor of 16. Aluminum has a thermal conductivity factor of 250.*
Our expert also pointed out that some other composite barrel systems on the market actually increase heat retention because they place insulating materials next to the inner steel barrel. (Carbon, Fiberglass, and Epoxy are all considered “insulating substances” as they have very low thermal conductivity*.) The LW system of aluminum over metal should avoid this mistake, our expert said. Lothar Walther says: “Unlike solid steel barrels, this barrel sheds heat fast. VERY FAST!”
Half the Weight of Conventional Barrels
How much weight can you save? With a 1.200″ shank diameter (except Savage) and a muzzle diameter of 0.850″, the LW Ultra-Lightweight Barrel is less than half the weight of a standard varmint barrel of the same size. Walther claims its UltraLight Barrel can be “carried for long distances and stand up to heavy firing.” This, LW says, makes these barrels “perfect… for varmint and tactical uses”.
Pre-Chambered Ultra-Lightweight Barrels Available in .22 to .338 Calibers
Lothar Walther offers Ultra-Lightweight barrels in a full range of calibers from .22LR to .338. Each Ultra-Lightweight Barrel comes complete with chamber, crown, and breech threads. These barrels are fluted by the factory. If you order a LW Ultra-Lightweight barrel, Lothar Walter provides the services of a specialist trained in building guns with these barrels. To order one of Lothar Walther’s bi-metal barrels, CLICK HERE or contact Lothar Walthar at the address below:Lothar Walther Precision Tools, Inc.
3425 Hutchinson Rd. – Cumming, GA 30040
Phone: 770-889-9998 | Fax: 770-889-4919
E-Mail: lotharwalther [at] mindspring.com
Website: www.lothar-walther.com
*Thermal conductivity is the quantity of heat transmitted through a unit thickness in a direction normal to a surface of unit area, due to a unit temperature gradient under steady state conditions. The factor values are based on this formula: W/(m.K) = 0.85984 kcal/(hr.m. °C). Here are thermal conductivty values for common materials: Aluminum, 250; Brass, 109; Steel (Carbon 1%), 45; Stainless Steel, 16; Carbon, 1.7; Brick dense, 1.3; Concrete (medium) 0.7; Epoxy, 0.35; Fiberglass, .04.
Story tip from EdLongRange. We welcome reader submissions.Similar Posts:
- Lothar Walther Bi-Metal Barrels Are Lighter, and Shed Heat Better
- Lothar Walther Offers Finished Garand and AR15 Barrels
- New Carbon-Wrapped Barrels from Helix 6 Precision
- Helix 6 Carbon-Wrapped Barrels — Pre-Fits and Blanks
- Metal Properties Revealed in ‘Guide to Gun Metal’
Share the post "Lothar Walther UltraLight Barrels — Less Heat, Half the Weight"
Tags: Aluminum, Composite Barrel, Fluted Barrel, Lothar Walther, Ultra-Light
I had a tac-sol barrel on my 10-22 that was built like this. Alum over SS. Seemed to work well.
I hope that in the future you will be able to publish additional detail on the method of assembly.
Since aluminum expands faster than steel as it warms, this might tend to loosen the fit between the two sections.
The Lewis Light Machine Gun employed an aluminum cooling radiator around the barrel, even incorporating fins to aid heat dissipation. Most experts agree, and my own experience confirms, that it did little or nothing that a bare barrel would not. These schemes always sound good but just don’t seem to work in practice. Josh may be onto something regarding differential thermal expansion. The more rapidly expanding aluminum may separate minutely along the interface, creating a thermal discontinuity.
I’d like to see some actual long string shot targets to see how accuracy is along with any kind of vertical dispersion.
reply to Josh & Steve:
the aluminium sleeve would undoubtebly be alloy, without knowing the exact making up expansion is hard to judge.
however that said, the sleeve and inner barrel would be a press fit at very high heat, much higher than we would ever see (unless we go sustained full auto)
Josh – The coefficient of thermal expansion for aluminium alloy is about 22 and steel between 10 and 18, if anything the effect of the higher thermal expansion ratio for aluminium alloy would result in the tightening of the fit between the two metal alloys. The expansion is in three dimensions remember, so for a tube this would result in the outer diameter increasing, and the inner diameter reducing, compressing the inner steel liner.
Concerning the varying rates of thermal expansion …
Aluminum sheds heat so much faster than stainless steel that it would always be cooler than the stainless steel liner, the liner being the source of the thermal energy. This would tend to offset the fact that aluminum expands more at a given temperature than steel.
As to the outer aluminum tube expanding inwards … I believe this is incorrect. I have personally heated pulleys to slip them over a shaft. The inner hole expands when heated.
Neil, Rick & Robert:
You boys need to review your thermodynamics texts. Only Robert got the expansion correct.
Steve, you are quite right, for starting tubes 10 mm in diamter changing from 20 to 120°C, the aluminium would expand to 10.0222 mm and the steel to 10.0173 mm, so a gap of 0.0049 mm (0.2 mils). Not much of a change, but a change none the less. Don’t know what I was thinking of?
I live in Columbus Ga. where it gets real hot. Here’s a tip to keep the heat down, just slide a copper pipe over that barrel melt some aluminum pour that into the pipe. Your good to go just saved you alot of $$$.
“.. a metals expert we contacted said that a bi-metal system employing fluted aluminum over steel, if assembled properly, could dissipate heat much better than steel alone (given the same diameter). Stainless steel has a thermal conductivity factor of 16. Aluminum has a thermal conductivity factor of 250.*”
Find another expert; there’s not going to be any useful improvement in heat dissipation.
Yes aluminum conducts heat better than stainless – but it’s not the thermal conductivity of the barrel metal that is limiting the cooling rate. The limiting factor is the thermal conductivity of the air layer/film surrounding the barrel (it is a *much* poorer conductor of heat than stainless) – and this is unchanged.
EDITOR: Some points. The air layer is not static, but moves over and around the barrel and is essentially infinite. Two, if what you say is correct, then why are heat sinks most often made from aluminum: “The most common heat sink materials are aluminium alloys. Aluminium alloy 1050A has one of the higher thermal conductivity values at 229 W/m•K but is mechanically soft. Aluminium alloys 6061 and 6063 are commonly used, with thermal conductivity values of 166 and 201 W/m•K, respectively.” Wiki. If you doubt that aluminum disperses heat more quickly, you can do your own experiment with cast iron and aluminum cookware. Any cook knows the answer to that one. Also, if the air layer’s thermal conductivity was the only limiting factor in heat dispersion then why do we even bother to insulate heating and cooling pipes at all? Likewise, if a metal’s thermal conductivity is irrelevant, then why do engine builders carefully select materials for radiators, engine fins, cooling lines etc. based on heat-dispersing properties (along with other factors).
Steve re read. I am stating that as per robs experience with pulleys, the alu sheath will need to be bought to high heat before the clearance is sufficient for press fitting. the hole will enlarge when heated… and shrink when cooled.
the complete process may likely involve cryo treatment of the barrel liner also.
The reason heat sinks are made from aluminum is that copper is expensive and gold is even more expensive. Heat sinks are shaped to present more surface area than the heat source to which they are attached. An aluminum barrel jacket of equal diameter to a homogeneous steel barrel will not transfer heat to the surrounding air any faster. It is limited by the air’s conductivity. Heat is simply trying to achieve equilibrium. When the barrel is hotter than the surrounding air, it will transfer heat to the air until they are the same temperature. Aluminum will transport the heat more quickly and the steel-aluminum barrel assembly will achieve stability faster but the barrel assembly will not lose heat to the air more quickly. Again, these schemes have been tried many times and simply do not provide a worthwhile benefit. Take a look at a Lewis Light Machine Gun barrel. It has large fins and many times the surface area of a conventional barrel and it did not appreciably improve the sustained fire rate. If it worked well, we would see many machine guns with finned, aluminum barrel jackets. Other than the Lewis, how many are there?
I’d certainly consider one for hunting…like a 16.5″ barrel on an action I could drop into a chassis stock when not shooting long distance.The weight savings would be attractive.
Forget fluting – it`s only for optic.
The Aluminium tube must be glued to the barrel with loctite – than it works well.