|
December 6th, 2014
Next time you have a barrel fitted, consider having your gunsmith create a “stub gauge” from a left-over piece of barrel steel (ideally taken from your new barrel blank). The outside diameter isn’t important — the key thing is that the stub gauge is created with the same reamer used to chamber your current barrel, and the stub must have the same bore diameter, with the same land/groove configuration, as the barrel on your rifle. When properly made, a stub gauge gives you an accurate three-dimensional model of the upper section of your chamber and throat. This comes in handy when you need to bump your case shoulders. Just slide a fired case (with spent primer removed) in the stub gauge and measure from base of case to the end of the gauge. Then, after bumping, re-measure to confirm how much you’ve moved the shoulder.

In addition, the stub gauge lets you measure the original length to lands and freebore when your barrel was new. This gives you a baseline to accurately assess how far your throat erodes with use. Of course, as the throat wears, to get true length-to-lands dimension, you need take your measurement using your actual barrel. The barrel stub gauge helps you set the initial bullet seating depth. Seating depth is then adjusted accordingly, based on observed throat erosion, or your preferred seating depth.
Forum member RussT explains: “My gunsmith [makes a stub gauge] for me on every barrel now. I order a barrel an inch longer and that gives him enough material when he cuts off the end to give me a nice case gauge. Though I don’t have him cut that nice-looking window in the side (as shown in photos). That’s a neat option. You can tell how much throat erosion you are getting from when it was new as well. For measuring initial seating depths, this is the most useful item on my loading bench next to calipers. Everyone should have a case gauge made by there smith if you have a new barrel put on.”
Forum member Lawrence H. has stub gauges made with his chamber reamers for each new barrel. He has his smith cut a port in the stub steel so Lawrence can actually see how the bullet engages the rifling in a newly-cut chamber. With this “view port”, one can also see how the case-neck fits in the chamber. Lawrence tells us: “My stub gauges are made from my barrels and cut with my chamber reamers. With them I can measure where my bullets are ‘touching the lands’ and shoulder bump dimensions. This is a very simple tool that provides accurate information.” To learn more about stub gauges, read this Forum Thread. The photos above and below show Lawrence’s stub gauges:
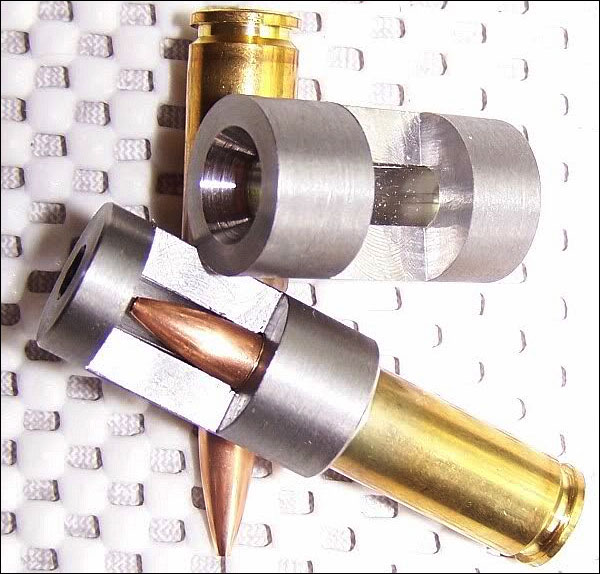
Share the post "Got Stub? Barrel Stub Gauges Serve Many Functions"
May 4th, 2014
Harrell’s Precision sells “semi-custom” full-length bushing dies for the PPC and 6BR chamberings. While the Harrell brothers do not cut the die to spec, they carry a large selection of dies made with slightly different internal dimensions. When you send in your fired brass, the Harrells choose a die from inventory with just the right amount of sizing (diameter reduction) at the top and bottom of the case. Given the quality, and precise fit, Harrell’s full-length dies are a good value at $75.00 plus shipping.
Bump Measuring Collar
The Harrell brothers provide a nice bonus item with each full-length die — a neat, little shoulder bump measuring device as shown in the photo at right. Hornady/Stoney Point sells a stand-alone tool that does the same job, but the Harrell’s bump collar is simpler and faster. To measure your shoulder bump, simply place the Harrell’s bump collar over the upper section of your deprimed case (before sizing) and measure the OAL with your calipers. The collar should seat on the shoulder without any wobble. After taking the measurement, then size the case in your full-length die, replace the collar and repeat the measurement. You want to set your die so the shoulder moves back about .001″ to .0015″ for most applications. (With semi-auto guns you may want more bump — .003″ or more.)
When measuring for shoulder bump, you need to remove the primers first. Our friend Boyd Allen explains: “Use a decapping tool or die to remove the fired primer before taking the initial measurement. When working to thousandths, even the raised edge of a crater or a slightly raised primer can throw you off by a significant amount.”
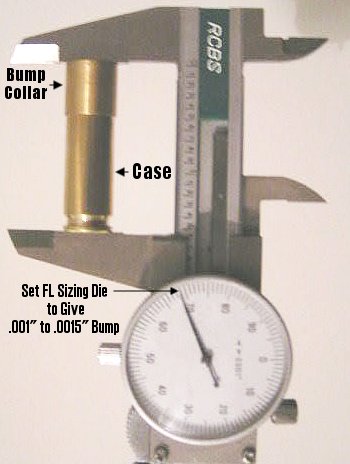
Share the post "Tech Tip: Measuring Shoulder Bump with Harrell’s Collar"
October 21st, 2012
Some of our readers have questioned how to set up their body dies or full-length sizing dies. Specifically, AFTER sizing, they wonder how much resistance they should feel when closing their bolt.
Forum member Preacher explains:
“A little resistance is a good, when it’s time for a big hammer it’s bad…. Keep your full-length die set up to just bump the shoulder back when they get a little too tight going into the chamber, and you’ll be good to go.”
To quantify what Preacher says, for starters, we suggest setting your body die, or full-length sizing die, to have .0015″ of “bump”. NOTE: This assumes that your die is a good match to your chamber. If your sizing or body die is too big at the base you could push the shoulder back .003″ and still have “sticky case” syndrome. Also, the .0015″ spec is for bolt guns. For AR15s you need to bump the shoulder of your cases .003″ – .005″, for enhanced reliability. For those who have never worked with a body die, bump die, or Full-length sizing die, to increase bump, you loosen lock-ring and screw the die in further (move die down relative to shell-holder). A small amount (just a few degrees) of die rotation can make a difference. To reduce bump you screw the die out (move die up). Re-set lock-ring to match changes in die up/down position.
That .0015″ is a good starting point, but some shooters prefer to refine this by feel. Forum member Chuckhunter notes: “To get a better feel, remove the firing pin from your bolt. This will give you the actual feel of the case without the resistance of the firing pin spring. I always do this when setting up my FL dies by feel. I lock the die in when there is just the very slightest resistance on the bolt and I mean very slight.” Chino69 concurs: “Remove the firing pin to get the proper feel. With no brass in the chamber, the bolt handle should drop down into its recess from the full-open position. Now insert a piece of fire-formed brass with the primer removed. The bolt handle should go to the mid-closed position, requiring an assist to cam home. Do this several times to familiarize yourself with the feel. This is how you want your dies to size your brass, to achieve minimal headspace and a nearly glove-like fit in your chamber.”
We caution that, no matter how well you have developed a “feel” for bolt-closing resistance, once you’ve worked out your die setting, you should always measure the actual amount of shoulder bump to ensure that you are not pushing the shoulder too far back. This is an important safety check. You can measure this using a comparator that attaches to your caliper jaws, or alternatively, use a sized pistol case with the primer removed. See Poor Man’s Headspace Gauge.
Share the post "TECH Tip: How to Set Your Dies for Correct Shoulder Bump"
September 21st, 2010
Here’s a word to the wise — not all full-length sizing dies are properly dimensioned to carry out the important task of “bumping” shoulders back on fired cases. With some dies the task may simply be impossible (without die or shell-holder modification). In fact, you may find that your attempt to bump the shoulder may actually INCREASE the dimension from base of case to shoulder datum!
We recently had some four-times fired 6mmBR Lapua brass. Using a Harrell’s collar that indexes off the shoulder, we measured the length from base of case to top of collar at 1.570″ (with primer removed). We noticed a little more resistance to bolt closure compared to fresh brass, so we decided to bump the shoulders back two thousandths. As a point of reference, we measured the same dimension (base of case to top of Harrell’s collar, primer out) as 1.5675″ on once-fired Lapua 6mmBR brass.
This Can’t Be Right …
To bump our shoulders we had an RCBS Gold Medal bushing full-length sizing die. Per the manufacturer’s instructions, we started with the die backed off 1/2 turn from contact with the shell-holder with the press ram at full height. We lubed and sized one case and then measured it. The shoulder had not moved. OK, no problem, we screwed the die down to contact the shell-holder (at full ram height) and tried again. This time the measured dimension was actually longer by a couple thousandths. The brass which measured (with collar) 01.570″ before sizing now measured 01.572″ — we were going in the wrong direction!
“Bumped” Shoulder Stretched .003″
Frustrated, we screwed the RCBS die in 1/8th turn past touching to allow “cam-over” which is necessary with some presses to actually push the shoulder back. We sized the case again, and this time the dimension had grown another .001″, to a total length of 1.573″! Wondering if there was something wrong with our calipers, we took the full-length sized brass (which previously had chambered just fine) to our 6BR rifle and tried to chamber it. Sure enough, the headspace had been lengthened by .003″ and the brass would not chamber at all.
Die Was Too Long Inside to Bump Shoulders Properly
What was going on? Here’s the explanation: the interior cavity of the die was too long so the shoulder surface inside the die was never actually making contact with the shoulder of the brass — and the die could not be screwed down any further. As the RCBS die, which was fairly tight in the bottom half, reduced the diameter of the brass, the case actually grew in length. While the brass was sized at the bottom it grew upwards because the “shoulder” section on the inside of the die was too high. As we “squeezed” the brass at the bottom it simply flowed upwards, increasing headspace.
With this RCBS die, in its current configuration, there was no way we could bump the shoulder back, even by .001″. The die would likely function effectively if we ground a few thousandths off the bottom, but we don’t think a die user should be obliged to make such a modification.
Lesson Learned: If your full-length die can’t bump your brass even when it is screwed down all the way (to cam-over if necessary), then you need a different die or you need to modify your die. As proof of this, we took out my trusty Redding 6mmBR full-length sizing die. This was set up (from experience), one-half turn off contact with the shell-holder. In that position, the Redding die easily bumped the shoulder of a fired case .002″ with no trouble whatsoever. We started at 1.570″ and ended up 1.568″ — right where we wanted to be. The task that couldn’t be done with the RCBS Gold Medal FL Die was accomplished easily with the Redding die. After lubing the case, we simply raised the ram to full height, and this moved the shoulder back .002″ as measured with the Harrell’s collar positioned on the shoulder.
Share the post "Bedeviled by Bump — When Full-Length Dies Don’t Work"
|